It goes without saying that any company manufacturing the majority of its products on an in-house basis is interested in further expanding its own production. At its headquarters and production site in Weng, in the north of Austria, Hargassner has therefore been investing in automation for some time – from the use of robots for sheet metal working to the introduction of driverless transport systems in its assembly department. The user-friendly operating software for its heating systems is also largely developed on site.
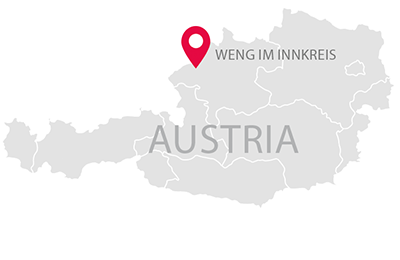