The slogan “This is forward” is central to the sustainability agenda of Coca-Cola Europacific Partners (CCEP) – the largest independent bottler of the Coca-Cola Company’s soft drinks. The agenda’s goals are ambitious. By 2030, the beverage producer is looking to achieve a 30 percent reduction in greenhouse gas emissions compared with 2019 – at its Genshagen plant and 13 other sites in Germany. By 2040, it is aiming to achieve climate neutrality. The focus is on packaging and raw materials. “For example, we are continuing to ramp up our business with reusable containers and want our airbag packaging to be made from 100 percent recycled PET. Production accounts for 9 percent of CO₂ emissions, and we are looking for optimisation potential in this area, too,” explains Quality and Food Safety Manager Florian Happe, who was also responsible for energy management at CCEP until 2021.
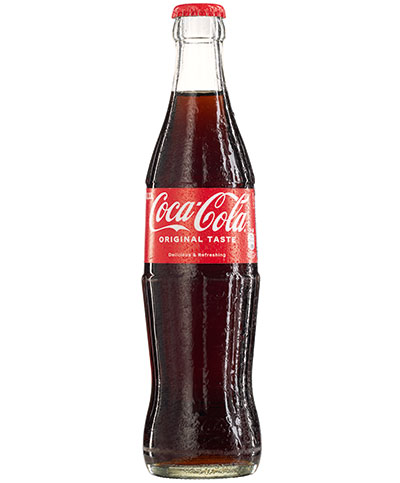
90 %
reduction in electricity consumption measured
> 400
cooling units from Rittal now ensure the correct operating climate at 14 CCEP sites.
9
months were required to install and commission all the replacement units.
2040
is the deadline the beverage producer has set itself to achieve climate neutrality.