I n not one but two locations – the United Kingdom and the Czech Republic – Cideon and the BDF team of digitalisation experts joined forces for the digital development of Schenck Process. SAP S/4HANA, SAP Engineering Control Center (SAP ECTR) and SAP Product and Process Governance (SAP PPG) were all rolled out at the same time for the market leader in material handling solutions and monitoring. Martin Schütz, Director Engineering EMEA and Project Leader Engineering at Schenck Process, explains: “Having analysed several options, our positive experiences with SAP PLM (CAD Desktop) and the opportunities offered by PPG and ECTR led us to opt for these solutions.”
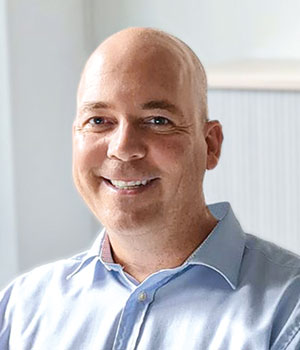
“Thanks to its partnership with Cideon and BDF, Schenck Process has reached an important international milestone.”
Martin Schütz,
Director Engineering EMEA, Schenck Process